Fuel level sensors play a critical role in various industries, ensuring accurate fuel measurement and providing crucial data to maintain smooth operations. From the automotive sector to marine and aviation, these versatile devices are indispensable in modern-day applications. This blog post will give you a comprehensive understanding of fuel level sensors, discuss their various types and applications, and provide maintenance tips to ensure optimum performance.
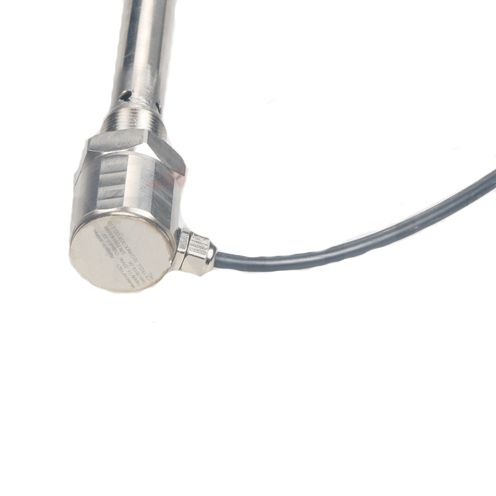
Types of Fuel Level Sensors
Float-based Sensors
Float-based fuel level sensors are the most common type and can be found in numerous applications. These sensors consist of a floating device, typically made of foam or other buoyant material, attached to a variable resistor or a potentiometer. As the fuel level changes, the float moves up or down, altering the resistance value and generating a signal proportional to the fuel level.
Capacitive Sensors
Capacitive fuel level sensors utilize the principles of capacitance to measure fuel levels. These sensors comprise two conductive plates, with the fuel acting as a dielectric medium between them. As the fuel level changes, so does the capacitance, producing a signal that reflects the current fuel level. Capacitive sensors are highly accurate and provide a reliable measurement in a variety of fuel types.
Ultrasonic Sensors
Ultrasonic fuel level sensors employ high-frequency sound waves to determine fuel levels. These sensors emit an ultrasonic pulse, which travels through the fuel and reflects off the surface. By measuring the time taken for the echo to return, the sensor can calculate the distance to the fuel surface and, consequently, the fuel level. Ultrasonic sensors are suitable for applications where contact with the fuel is undesirable or infeasible.

Applications of Fuel Level Sensors
Automotive Industry
Fuel level sensors are a crucial component in most vehicles, responsible for providing real-time fuel level data to the driver. They help ensure safe and efficient operation by alerting the driver when fuel levels are low or when it’s time to refuel. Additionally, they contribute to fuel economy by providing accurate data to the vehicle’s engine management system.
Marine and Aviation
In the marine and aviation industries, accurate fuel level measurement is paramount for safety and efficient operation. Fuel level sensors are utilized in boats, ships, and aircraft to monitor fuel consumption and remaining fuel levels. They help prevent incidents caused by fuel shortage and aid in optimizing refueling intervals.
Industrial Applications
Fuel level sensors are also utilized in various industrial applications, such as bulk fuel storage and fuel distribution systems. These sensors ensure accurate fuel inventory management, help detect leaks, and enable remote monitoring for enhanced efficiency and safety.
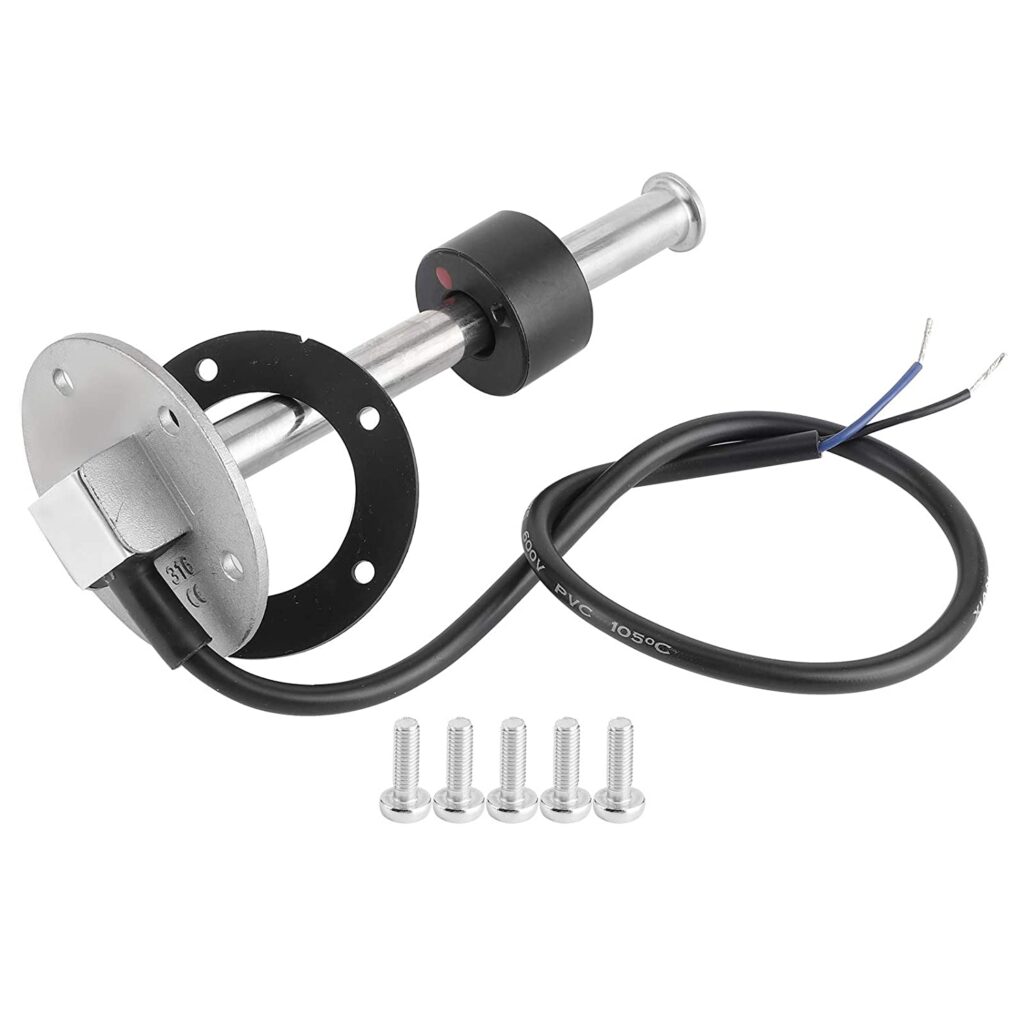
Maintenance Tips for Optimum Performance
Regular Inspection
Regularly inspect your fuel level sensor for any signs of wear, corrosion, or damage. Check the electrical connections and wiring for any loose connections, frayed wires, or signs of water ingress. Inspecting your sensor will help you identify potential issues before they escalate, ensuring reliable operation.
Clean and Calibrate
Ensure your fuel level sensor is clean and free from any debris or contaminants that may affect its performance. This is particularly important for capacitive and ultrasonic sensors, as contaminants can impact the accuracy of the measurements. Periodically calibrate your sensor to maintain its accuracy and reliability.
Replace Worn or Damaged Components
If you notice any signs of wear or damage during your inspections, promptly replace the affected components. For float-based sensors, this may involve replacing the float or the variable resistor. For capacitive and ultrasonic sensors, this could mean replacing the sensing element or associated electronics.
Seek Professional Assistance
If you encounter persistent issues with your fuel level sensor or are unsure about the maintenance procedures, it is highly recommended to seek professional assistance. A qualified technician can diagnose and resolve any problems, ensuring your sensor operates optimally and provides accurate fuel level readings. By maintaining a close relationship with a professional service provider, you can also benefit from expert advice on sensor selection, installation, and maintenance.

Conclusion
Fuel level sensors are vital components in a wide range of applications, providing accurate and real-time data for optimal operation and safety. Understanding the different types of fuel level sensors, their applications, and maintenance tips is essential for those who depend on these devices. By regularly inspecting, cleaning, calibrating, and replacing worn components when necessary, you can ensure your fuel level sensor remains reliable and accurate. And when in doubt, never hesitate to seek the expertise of a qualified professional to help maintain and optimize your sensor’s performance.